Analysis of the Main Structural Components and Functions of Spider Couplings: From Components to Performance Advantages
In factory workshops, spider elastic couplings are almost like "permanent guests" in transmission systems. Among our company, Xinde's, total sales last year, the shipment volume of these couplings ranked among the top three in the coupling category. However, many customers often ask during the selection process: Why do some couplings last three to five years without failure, while others frequently malfunction, even though they look similar in appearance? Now, let Xinde's technical team take you through a detailed breakdown of the main components of spider couplings, revealing the technical logic behind their material selection and functional design to assist you in selection and maintenance.
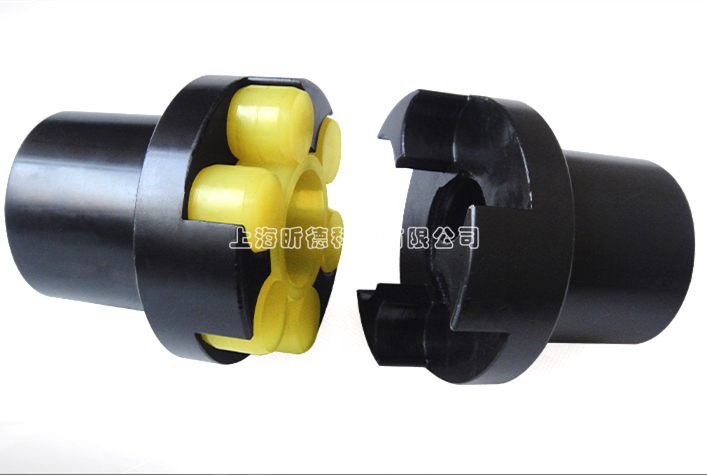
I. Main Structural Components of Spider Couplings
Spider couplings consist of three parts: two metal half-shaft sleeves and an intermediate spider-shaped elastic element. These three components work in harmony to achieve torque transmission, axial/radial compensation, and vibration attenuation functions.
1. Two Half-Shaft Sleeves: Rigid Connection and Precise Positioning
Material Selection:
Half-shaft sleeves are typically made of high-strength aluminum alloy or high-quality alloy steel.
-
Aluminum Alloy: It has a low density and strong corrosion resistance, making it suitable for light-load, high-speed applications (such as textile machinery and office equipment).
-
Alloy Steel: It offers high torsional strength and wear resistance, suitable for heavy-load, low-speed operating conditions (such as metallurgical equipment and construction machinery).
Functional Analysis:
-
Torque Transmission: The sleeves are rigidly connected to the driving and driven shafts through keyways or clamping screws, ensuring lossless power transmission.
-
Axial/Radial Compensation: The clearance design between the inner bore of the half-shaft sleeve and the shaft can absorb minor axial displacements (±0.1mm) and angular deviations (±1°), extending the service life of the equipment.
-
Positioning Accuracy: The precisely machined inner bore of the sleeve provides an interference fit with the shaft, ensuring the coaxiality of the transmission system and reducing operational noise.
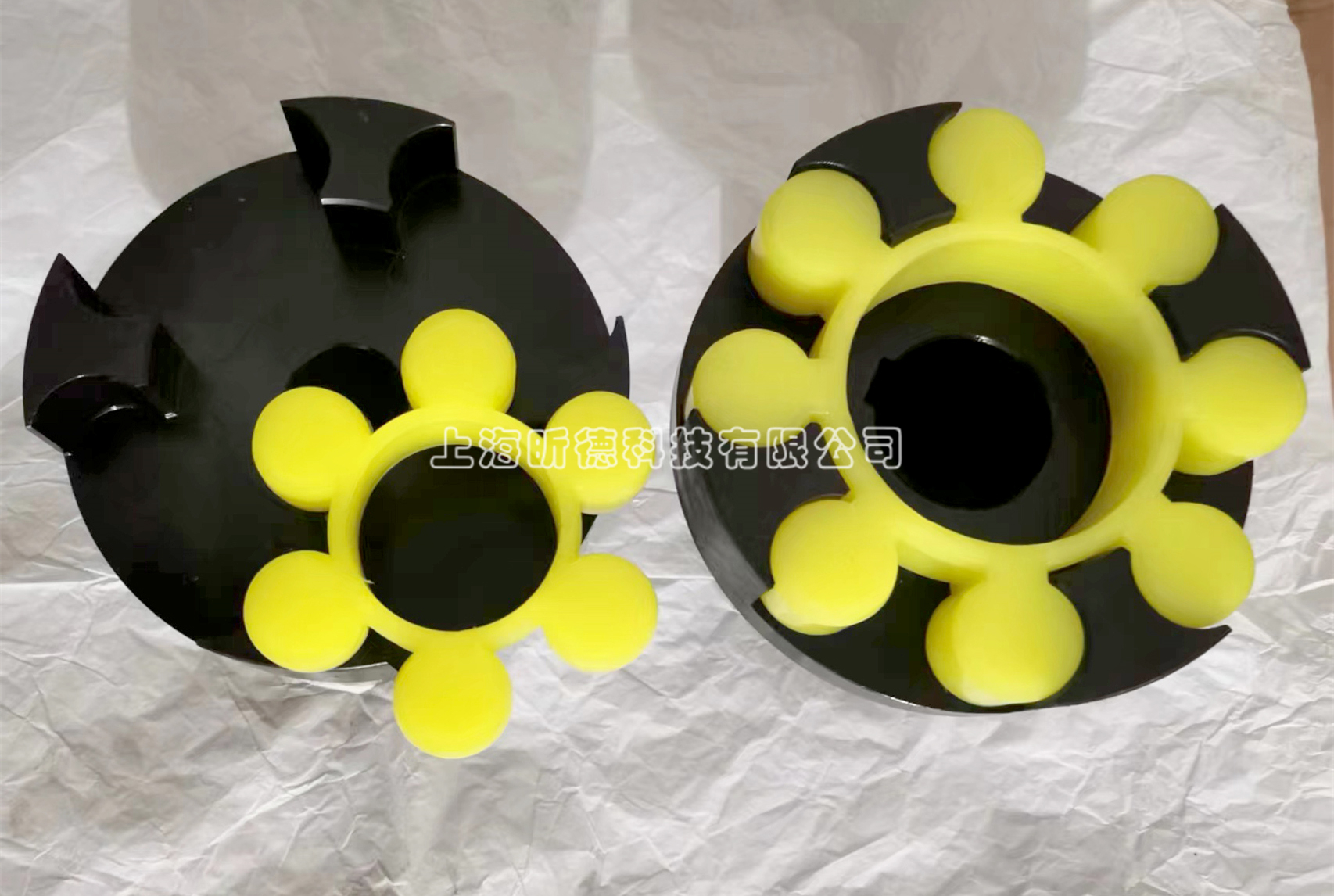
2. Spider-Shaped Elastic Element: Shock Absorption and Vibration Damping
Material Selection:
The elastic element is mostly made of polyurethane (PU) or nitrile rubber (NBR), with some high-end models using hydrogenated nitrile rubber (HNBR).
-
Polyurethane: It has excellent wear resistance and high tear strength, suitable for medium- to high-speed applications (such as servo motor transmissions).
-
Nitrile Rubber: It offers outstanding oil resistance, suitable for lubricated environments (such as hydraulic equipment and printing machinery).
-
Hydrogenated Nitrile Rubber: It can withstand high temperatures (-20℃~150℃) and chemical corrosion, suitable for extreme operating conditions (such as chemical pumps and new energy equipment).
Functional Analysis:
-
Vibration Attenuation: The spider-shaped structure absorbs impact loads through elastic deformation, reducing the risk of equipment resonance.
-
Overload Protection: When the torque exceeds the rated value, the elastic element deforms and breaks first, preventing rigid damage to the transmission system.
-
Electrical Insulation: The rubber material can block shaft currents, preventing electrical corrosion of motor bearings (especially suitable for variable frequency motors).
II. Structural Advantages and Key Selection Points
-
Zero-Backlash Transmission: The close fit between the half-shaft sleeves and the elastic element eliminates the backlash found in traditional couplings, improving the response speed of servo systems.
-
Maintenance-Free Design: The fully mechanical structure requires no lubrication, reducing maintenance costs.
Selection Recommendations:
-
Rotational Speed: For high-speed applications, prioritize aluminum alloy sleeves combined with polyurethane elastic elements (rotational speed ≤ 6000rpm).
-
Temperature: For high-temperature environments, choose HNBR elastic elements (-40℃~150℃).
-
Eccentric Compensation: When the angular deviation exceeds 1°, it is recommended to use a diaphragm coupling in combination.
III. Application Scenarios and Technical Extensions
Spider couplings are widely used in:
-
CNC Machine Tools: They ensure precise synchronization between the spindle and servo motor.
-
Automated Production Lines: They absorb the frequent start-stop impacts of robot joints.
-
New Energy Equipment: They adapt to the dynamic loads of wind turbine gearboxes and photovoltaic tracking systems.
Technical Trends:
With the development of Industry 4.0, lightweight design (carbon fiber sleeves) and intelligence (embedded sensors to monitor the lifespan of elastic elements) are becoming the upgrading directions for spider couplings.
The performance of spider couplings mainly lies in the balanced design of the rigid support provided by the two half-shaft sleeves and the flexible cushioning offered by the spider-shaped elastic element. When selecting a coupling, it is essential to comprehensively consider three major factors: load, rotational speed, and environment, and match the material and structural parameters to achieve optimal efficiency and reliability of the transmission system. For customized solutions or technical consultations, please feel free to contact our professional engineers at Shanghai Xinde for support.